Азот
Актиний
Алюминий
Америций
Аргон
Астат
Барий
Бериллий
Берклий
Борий
Бор
Бром
Ванадий
Висмут
Водород
Вольфрам
Гадолиний
Галлий
Гафний
Гелий
Германий
Гольмий
Дармштадтий
Диспрозий
Дубний
Европий
Железо
Золото
Индий
Иод
Иридий
Иттербий
Иттрий
Кадмий
Калий
Калифорний
Кальций
Кислород
Кобальт
Кремний
Криптон
Ксенон
Кюрий
Лантан
Литий
Лоуренсий
Лютеций
Магний
Марганец
Медь
Мейтнерий
Менделеевий
Молибден
Мышьяк
Натрий
Неон
Нептуний
Неодим
Никель
Ниобий
Нобелий
Олово
Осмий
Палладий
Платина
Плутоний
Полоний
Празеодим
Прометий
Протактиний
Радий
Радон
Резерфордий
Рений
Рентгений
Родий
Ртуть
Рубидий
Рутений
Самарий
Свинец
Селен
Сера
Серебро
Сиборгий
Скандий
Стронций
Сурьма
Таллий
Тантал
Теллур
Тербий
Технеций
Титан
Торий
Тулий
Углерод
Уран
Унунбий
Фермий
Фосфор
Франций
Фтор
Хассий
Хлор
Хром
Цезий
Церий
Цинк
Цирконий
Эйнштейний
Эрбий
|
|
|
|
|
Углерод
|
История |
Свойства |
Применение |
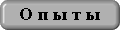 |
Символ - С |
Атомный вес - 12.011 |
Плотность - 1.85 |
Возгоняется при 3500 °C |
|
Известен с глубокой древности. |
|
|
|
|
Углерод является одним из основных элементов, формирующих жизнь на Земле, и об одном этом можно было бы говорить достаточно долго.
Но поскольку моя коллекция относится к области неорганической химии, я ограничусь только образцами аллотропных модификаций этого элемента.
|
Образец, который я сделал для компактного варианта таблицы, это один грамм синтетических алмазов, запаянных в ампулу
(ну, или пять карат, так как обычно массу алмазов измеряют в каратах, а драгметаллов – в унциях ). Подробнее об этих алмазах написано чуть дальше.
|
Попытки синтезировать алмаз из графита предпринимал еще Бриджмен (который также открыл черный фосфор и вообще известен работами в области высоких давлений).
Но Бриджмену получить алмазы не удалось, зато удалось ученым в Швеции и компании «General Electric».
Первые раньше получили алмазы, вторые первыми опубликовали результаты.
В настоящее время алмазы производятся в беспрессовых аппаратах типа «разрезная сфера» («Split Sphere»).
Производство алмазов налажено во многих странах, в том числе и в России, поэтому первой мыслью было попробовать найти и «поддержать» российского производителя.
Но не тут-то было. По интернету я нашел три фирмы, которые продают абразивные порошки на основе синтетических алмазов.
Кажется, одна из них производит алмазы сама, остальные – дистрибьюторы.
Послал во все три фирмы письма, в которых писал, что хотел бы приобрести 10–20 грамм (50–100 карат) самого крупного алмазного порошка (500–600 мкм, или 30–35 mesh).
И все... Целый месяц ни ответа, ни привета.
Через месяц ответили из одной фирмы – написали, что могут продать только крупную партию (больше 1000 карат), и цена будет составлять полтора доллара за карат (ну и на том спасибо, что ответили, из других двух вот уже два года нет никаких вестей).
В общем, надо покупать слишком много и слишком дорого, а еще, как только на той фирме узнали, что купить хочет физическое лицо и за наличные, сразу же отказались продавать.
Ладно, не хотите как хотите, на российских производителях свет клином не сошелся. Набираем в Google.com поиск картинок по фразе "Synthetic diamonds" и жмем на наиболее понравившуюся картинку (примерно такую, как третья фотография на этой странице).
Ссылка ведет на сайт китайской компании, одного из ведущих производителей алмазных абразивных материалов.
Ищем на сайте ближайшего дилера (для меня ближайшим оказалась немецкая фирма), пишем ему запрос (такой же, как и в российские фирмы, только на английском языке).
Ответили в течение часа, обговорили детали пересылки, оплаты, и через пять дней я достал из почтового ящика конверт с 20 граммами алмазов, которые можно видеть на фотографии.
В результате, алмазы обошлись в два раза дешевле (за карат), чем просили в России.
|
Алмазный порошок выглядит как ярко-желтый сверкающий песок, а если поместить его под микроскоп, видно, что он состоит из хорошо ограненных кристалликов (в основном, кубооктаэдров).
От формы кристаллов и их совершенства зависит сорт и цена абразивного порошка.
Чем более «округлые» и совершенные кристаллы в абразиве, тем большую нагрузку они могут выдержать без разрушения и тем долговечнее абразив (и тем для более тяжелых работ его можно применять).
Размер клеточки на фото – полмиллиметра.
|
Ну, продолжим про алмазы, на этот раз – про природные.
Хорошо известно, что цена алмазов сильно зависит от их размера, причем зависимость не прямо пропорциональная, а квадратичная.
То есть, камень в два раза большего веса будет стоить в четыре раза дороже.
Эта зависимость работает для камней среднего размера и одинакового качества. От качества алмаза его цена зависит не меньше.
Например, ограненный бриллиант хорошего качества, весом в карат, стоит около 10000 долларов, а необработанный непрозрачный камень с трещинами может стоить на два–три порядка меньше.
На фотографиях – настоящие бриллианты, но достаточно низкого качества.
Они тоже здорово блестят и переливаются на свету, но если взглянуть на них «вооруженным» глазом, видно, что они содержат много включений и трещин.
Общий вес всех бриллиантиков – около 0.3 карата (60 мг).
При желании, такую же кучку можно найти на ebay.com, долларов за 20–30.
|
Пример необработанного природного алмаза. Вес – 0.95 карата.
|
Я встречал классификацию алмазного инструмента с разделением на абразивный и однокристальный.
Вот это – типичный пример однокристального алмазного инструмента. Алмазный резец (если не ошибаюсь, проходной, но торцевать им тоже можно).
Тут к алмазу так же предъявляются определенные требования, но они не настолько строгие, как в случае ювелирных алмазов.
Кристалл, из которого делают резцы (а также алмазные скальпели, стеклорезы, фильеры и т.п.), может быть мутным, окрашенным, но в нем не должно быть трещин.
Алмазные резцы и фрезы используются для обработки цветных металлов, пластмасс, армированных композитов, а вот сталь такими резцами точить не стоит.
Углерод прилипает к режущей кромке кристалла и отрывает от неё осколки, портя резец.
Зато на обработке, например, пластиков, алмаз может работать без перезаточки практически вечно и дает очень чистую, практически зеркальную поверхность.
Кстати, этому способствует высокая теплопроводность алмаза, которая помогает отводить тепло от обрабатываемого изделия.
Если спросить, какой материал обладает самой высокой теплопроводностью, большинство людей ответит: серебро.
Это не так. После сверхтекучего гелия, который обладает самой высокой теплопроводностью (но, правда, существует только при температуре ниже 2.17 Кельвина), лучше всего проводит тепло алмаз.
Его теплопроводность в двадцать раз выше, чем у серебра.
Кстати, как это ни смешно, но синтетические алмазы иногда используют как теплоотводы в полупроводниковой технике,
правда небольшой (5х5х1 мм) кристаллик, используемый для этих целей, стоит около 250 евро.
|
Графитовый блок. Графит это, пожалуй, самая используемая в технике форма углерода.
Он встречается и в самородном виде, но для технических применений чаще используется синтетический графит.
Электроды для дуговых печей и электролизеров, замедлитель в ядерных реакторах, материал тиглей и лодочек для плавки металлов, футеровка химических аппаратов, материал нагревательных элементов, уплотнения – вот далеко не полный список применений графита.
Графит обладает высокой теплопроводностью и очень устойчив к перепадам температуры, (то есть, например, раскаленный тигель из графита можно быстро охладить и он не треснет).
Графит очень легко поддается механической обработке и из него удобно вырезать формочки для отливки легкоплавких металлов.
Графитовые блоки можно легко точить и фрезеровать даже на небольших настольных станках.
Правда, надо следить, чтобы выбранный для обработки графит был чистым и не содержал глины, иначе резцы достаточно быстро тупятся.
|
Предыдущий образец графита получен прессованием графитового порошка, и поэтому он анизотропен.
А вот на этом фото – кусочки пиролитического графита. Его получают разложением летучих углеродосодержащих соединений на поверхностях, нагретых до высоких температур (пиролизом).
При таком способе получения кристаллы графита растут ориентированно, и поэтому пиролитический графит обладает сильно выраженной анизотропией.
Ну, например, его можно так же легко, как слюду, расщепить на более тонкие листочки.
|
А еще с пиролитическим графитом можно провести интересный опыт.
Графит является одним из самых сильных диамагнетиков (еще висмут и сверхпроводники), причем магнитная проницаемость у графита зависит от направления (диамагнетизм максимально выражен в направлении, перпендикулярном слоям),
поэтому если тонкую пластинку графита поместить над сильными магнитами, она будет левитировать на высоте в пару миллиметров.
|
На следующих трех фотографиях представлены различные изделия из стеклоуглерода.
Не уверен, что его можно назвать аллотропной модификацией углерода, но одной из разновидностей – вполне.
Стеклоуглерод обладает свойствами, которые делают его очень хорошим материалом для изготовления тиглей.
Он устойчив на воздухе до температуры 500–600°C, а в вакууме – до 2500°C.
Не реагирует с большинством минеральных кислот, расплавами многих полупроводниковых соединений, а также таких металлов, как золото, серебро, медь.
Обладает низкой газопроницаемостью и высокой устойчивостью к перепадам температуры.
А вот найти технологию производства стеклоуглерода оказалось не очень просто.
В большинстве источников в российском интернете написано, что он образуется при пиролизе углеродосодержащих веществ.
Но поскольку таким образом получают и графит, и кокс, и сажу, интересно было бы узнать более точные условия.
На сайтах иностранных фирм – производителей изделий из стеклоуглерода написано, что процесс сложный, занимает чуть ли не месяц и является коммерческой тайной...
В общем, я решил попробовать поискать в научных статьях.
В результате нашел следующее: впервые эту форму углерода получили в 1963 году сотрудники английской компании «Plessey» J. C. Lewis и F. C. Cowlard.
Но в статье опять же написано, что они получили стеклоуглерод прокаливанием «определенных форм углерода в нейтральной среде при температуре 2000°C», а так же сообщают, что более подробная методика не публикуется, поскольку они в данный момент оформляют патент на это изобретение.
Самый первый патент мне найти не удалось, но в одном из следующих (этих же авторов) приведен такой вариант «улучшенной методики получения стеклоуглерода»:
Тонкостенное изделие из фенолформальдегидной смолы отверждают при температуре 160°C.
Затем нагревают его до температуры 890°C в инертной атмосфере в течение 7–12 дней и охлаждают до 300°C.
Следующую стадию нагрева до 1800°C проводят в вакууме в течение 3 дней, и после охлаждения получают изделие из стеклоуглерода.
В более поздних патентах можно также найти более быстрые способы получения этого материала.
|
На первом фото был стеклоуглеродный тигель, а на этих фото – сферический стеклоуглеродный порошок.
После модификации поверхности органическими группами, его можно использовать как сорбент в различных процессах.
|
Фуллерены это одна из самых «новых» аллотропных модификаций углерода.
Впервые они были обнаружены в 1985 году, а затем получены в препаративных количествах испарением графита в атмосфере гелия.
В настоящее время это один из основных методов получения фуллеренов.
Метод сам по себе не очень сложный, но полная процедура выделения чистых фуллеренов из смеси (при испарении образуется смесь C60 и C70 с небольшой примесью других фуллеренов) достаточно трудоемкая. Поэтому в настоящее время цена на фуллерены достаточно высока и составляет примерно 25$ за грамм C60 чистотой 99.5%. C70 дороже и стоит около 270$ за грамм 98% фуллеренов.
При попытке купить немного фуллеренов в России меня ждало такое же разочарование, как и с алмазами.
Во-первых, в России фуллерены продает только одна фирма в Санкт-Петербурге (они не желают иметь дела с частными лицами, принимают только оплату по безналичному расчету и не пересылают фуллерены по почте),
а во-вторых, по неведомым мне причинам, их цены на 10–20% превышают цены в американских фирмах (которые принимают разные типы оплаты, готовы продавать фуллерены любому, кто готов платить за них, и могут переслать товар в любую страну).
Поэтому, скорее всего, придется заказывать большее количество фуллеренов именно там.
|
Еще одна модификация углерода, которая по своему строению похожая на фуллерены, называется нанотрубки.
Если молекула фуллерена по форме напоминает мячик,
молекулы нанотрубок имеют форму именно полых трубок, стенки которых состоят из атомов углерода.
Внешне, нанотрубки предстявляют собой аморфный порошок глубокого черного цвета.
Те нанотрубки, стенки которых состоят из одного слоя атомов углерода называются одностенными нанотрубками (SWNT, single wall nanotubes),
но существуют так же молекулы, в которых несколько углеродных трубок разного диаметра как бы вставлены одна в другую.
Такие молекулы называют MWNT (multi wall nanotubes) (по Русски наверное будет многостенные нанотрубки, хотя английский вариант мне встречался чаще).
На фото - SWNT.
|
Углепластики, это композитные материалы, получившие широкое распространение за последние двадцать лет,
хотя в таких отрослях, как авиакосмическая, они применяются еще с семидесятых годов прошлого века.
В настоящее время, из этих композитных материалов делают детали спортивного инвентаря,
каркасы авиамоделей и многие другие детали, дял которых необходимо иметь малый вес при высокой прочности.
На фото - небольшой авиамодельный винт весом всего двести миллиграмм.
По своему строению, углепластик (по английски Carbon fiber reinforced polymer) похож на копмозитные материалы на основе стекловолокна (стеклопластики),
но вместо стеклянных волокон используются углеродные.
Поскольку углеродное волокно обладает очень высокой прочностью на разрыв и низкой плотностью,
после армирования им полимеров, получается очень легкий материал, по прочности превосходящий некоторые сорта стали.
Разумеется у этого замечательного материала есть и свои недостатки, которые препятствуют его повсеместному применению.
Во первых это достаточно высокая цена обусловленная сложностью получения как самих углеродных волокон так и готовых изделий из углепластика.
Во вторых, полимеры связывающие углеродные волокна, могут деградировать под действием солнечного света и прочность материала будет снижаться.
Не смотря на то, что углеродное волокно обладает исключительной термостойкостью и может выдерживать температуры выше тысячи градусов,
термостойкость углепластиков определяется полимерным связующим (то есть, как правило, не превышает 200-300 °C).
Ну и так же, поврежденные изделия достаточно сложно отремонтировать с сохранением прежнего вида.
Существует несколько способов производства деталей из углепластиков.
Один из них, используемый например в производстве корпусов или других объемных деталей,
включает в себя:
изготовления прототипа корпуса (например из дерева, пенопласта или алюминия)
покрытие прототипа разделительным слоем (например воском), который не дает полимерному связующему прилипать к модели
нанесение связующего (напрмер эпоксидной смолы)
накладывание нескольких слоев углеродной ткани с промазыванием каждого слоя смолой
прижимание и выравнивание всех слоев вакуумной оболочкой с последующим отверждением смолы.
|
Как было написано выше, полимерная связка органичивает максимальную
рабочую температуру углеродного волокна, хотя и придает материалу гибкость.
Но что делать, если хочется использовать жаропрочные свойства углеродных волокон полностью?
Один из вариантов решения можно видеть на фото. Это трехмерный композитный углеродный материал.
Он получен первоначальным сплетением углеродных нитей в трехмерную конструкцию,
которая затем пропитывается например расплавленным кремнием.
При реакции кремния с углеродом образуется карбид кремния,
который придает материалу твердость и устойчивость к окислению кислородом воздуха при высоких температурах.
Полученный материал хрупок, но зато выдарживает нагрузки при температурах
больше полутора тысяч градусов и использовался например в элементах конструкции космического корабля "Буран".
|
Сам по себе, графит это довольно хрупкое вещество,
но после специальной обработки, можно превратить его в гибкий материал, из которого можно делать всевозможные термостойкие прокладки и уплотнения.
На фото - как раз результат такой обработки - графитовая фольга.
Как известно, графит имеет слоистую структуру и в определенных условиях,
между этими слоями можно "впихнуть" некоторое количество атомов металлов, остатков неорганических кислот и т.п.
Если некоторое время нагревать графит например с хромовой смесью,
а потом с серной кислотой, "влезшие" молекулы вызовут разбухание графита
и получится так называемый "терморасширенный графит".
Его можно спрессовать в фольгу, прокладки, шнуры и прочие уплотнительные изделия.
Они не содержат асбеста, то есть не опасны для здоровья, термо- и химически стойки, долговечны.
|
|